Diaphragm wall equipment is frequently used on large urban projects such as subway stations. Since these construction sites are located in densely populated areas and often last for several years, negative impacts such as traffic restrictions, noise, dust and exhaust emissions are a significant factor. Increasingly strict regulations demand resource-efficient work, reduced local CO2 emissions and minimised noise pollution. Additionally, tight spatial conditions pose major challenges for both people and machinery.
With that in mind, Bauer has introduced its new BCS 185 power pack, which features a modular drive concept. This system relies on a flexible drive power pack, allowing operators to choose between an electric motor and a diesel unit. Thus the cutter system can be operated electrically with no local emissions or conventionally with diesel. Depending on the site conditions, the power pack can also be positioned on the side, rear or even apart from the machine to minimise the required space.
Another highlight is that the BCS 185 power pack produces less noise pollution. The diesel HD 1400 can be equipped with a Silent Kit, while the HE 1400 electric power pack is particularly quiet thanks to its low-noise electric motor.
According to Bauer, the BCS 185 power pack is currently working on the Grand Paris Express project. Here, diaphragm walls are being constructed at depths of up to 80 m. Thanks to its compact design and rapid operational readiness, the system enables efficient operations under challenging conditions. Until 2027, it will be used on multiple stations for Line 15.
With the new BCS 185 power pack, Bauer offers a flexible and sustainable solution for diaphragm wall construction. This innovation makes it possible to adapt the equipment optimally to the specific project requirements and represents an important step towards an emissions-free construction site.
All images: Bauer Group
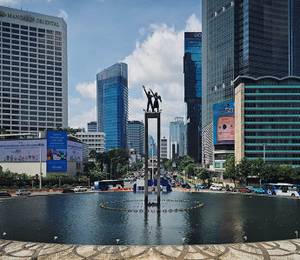
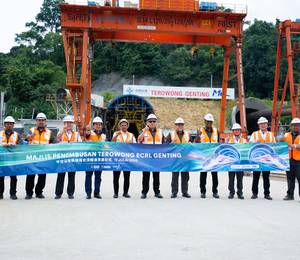
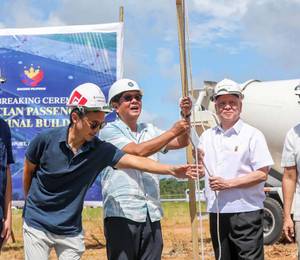
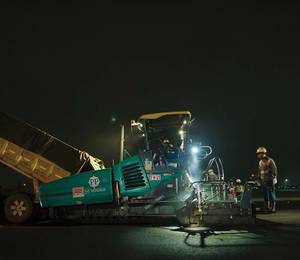
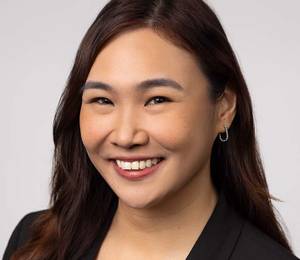
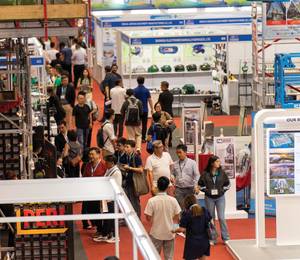
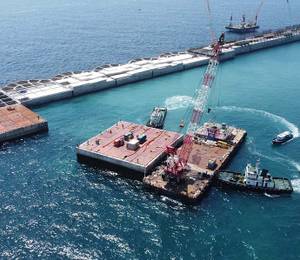